BACKGROUND TO NEW INDUSTRY STANDARDS
WHY IS SCANIA CHANGING?
Scania is taking a big step in its digitalization journey by transitioning to industry standards. Scania is updating its IT landscape and general ways of working to enable strategic growth ambitions – to make the organization future proof and make Scania a more attractive partner to work with. These changes will make it easier to meet the demands of the future, serving the customers of today with better prediction in delivery.
WHAT IS IN IT FOR SUPPLIERS?
Scania aspires to develop a modern supply chain collaboration hub in close partnership with suppliers through an optimized supplier experience with improved data visibility and traceability of deliveries throughout the Scania Supply Chain. Scania is introducing a global standardized way of working based on OEM & industry best practice to reduce complexity and enable the introduction of a user-friendly and future-proof system landscape.
Implications for suppliers
Scania is implementing a new ERP (Enterprise Resource Planning) system and global standardized way of working as the foundation for administrative and transactional processes within Industrial Operations. These changes includes changes to the current EDI setup and label formats impacting suppliers.
Overview of key changes
- Updates to EDI landscape
Based on industry benchmarks, Scania introduces new and improved EDI messages (for Delivery Schedule, Advanced Shipping Notice (ASN), and Invoice). This will require IT changes in your end. You can read more about the formats in the technical specifications and logistics manual (STD-4172-1).
- Updates to transport labels
Scania is introducing a new label, the Global Transport Label (GTL). The GTL must contain a unique identifier number (HU) for outer and inner packaging level. This number needs to be applied to the ASN and the labels of all goods that are sent to Scania. You can read more about the new format in the technical specifications and logistics manual (STD-4172-10).
- Introduction of scheduling agreement
The scheduling agreement is used for automatic matching of invoices and in goods reception and consists of a list of prices and parts and is intended as an extension to the current contract. The current contract remains the valid legal document. A new supplier ID and part numbers are introduced.
Onboarding journey and timeline
A implementation plan is outlined for you as a supplier, and you will be supported through this journey by our Supplier Readiness Team. You as a supplier is expected to comply and make sure to follow timelines and set deadlines.
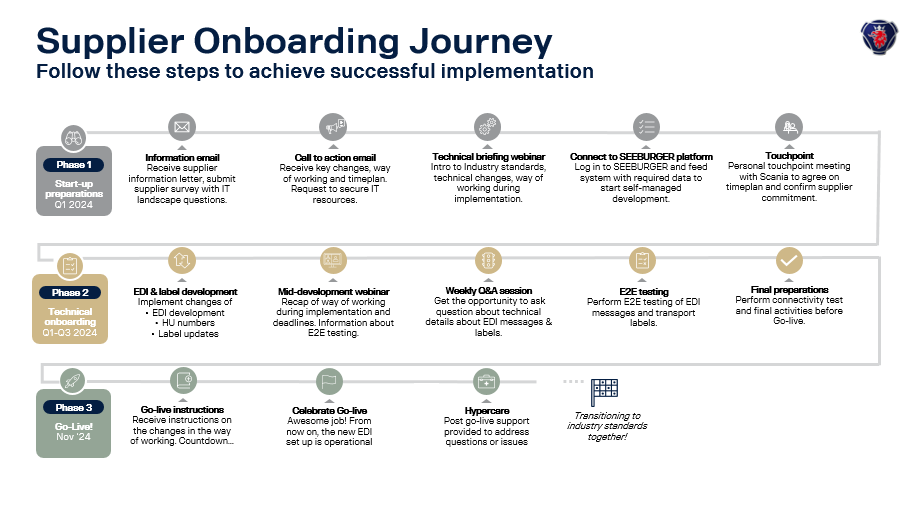
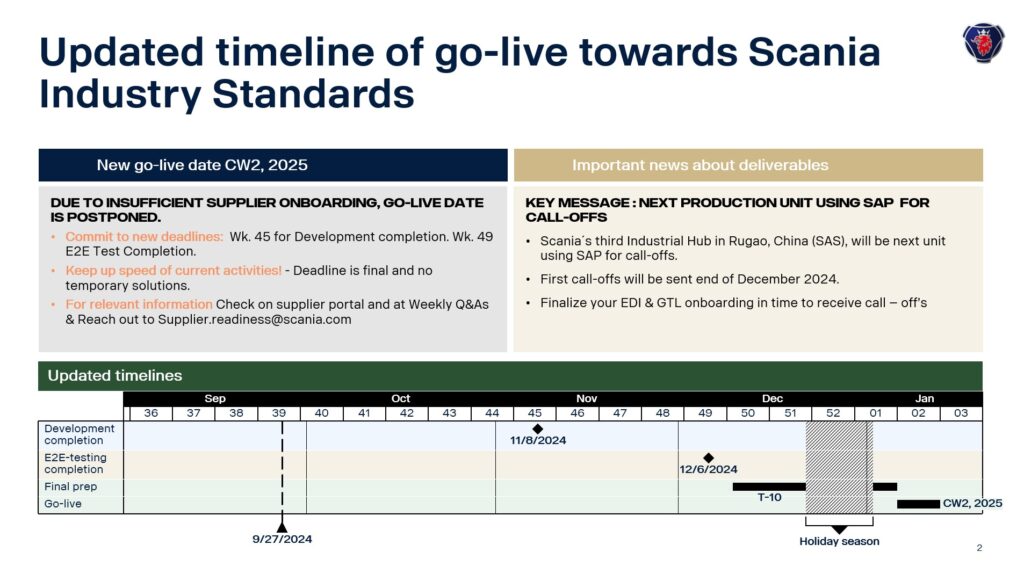
INDUSTRY STANDARDS OUTLOOK
This implementation will continue in the upcoming years and all automotive parts suppliers working with Scania will eventually be impacted. Please note that you will be notified by Scania once you are in scope for the transition to industry standards.
The first Industry Standards releases took place in the Battery Factory in Södertälje in 2023. The next phase takes place in 2024 and applies for all automotive parts deliveries for serial production to Scania via Hasselt Logistic Hub Central Europe, Logistic Center & Consolidation Point.
Classic EDI Supplier Information Letter | 25 Oct, 2024 |
Vision and Mission | 27 Aug, 2024 |
Supplier-Onboarding-Journey | 27 Aug, 2024 |
WebEDI Supplier Information Letter | 25 Oct, 2024 |