EDI@SCANIA
The simple definition of EDI (Electronic Data Interchange) is a standard electronic format that replaces paper-based documents. By automating paper-based transactions, organizations can save time and eliminate costly errors caused by manual processing. As a supplier to Scania, you are required to use EDI. Scania uses EDIFACT messages and the Odette Transport Label (OTL) for electronic communication with our supplying organisations.
EDI support for Scania Suppliers is handled by tps_scania@seeburger.de.
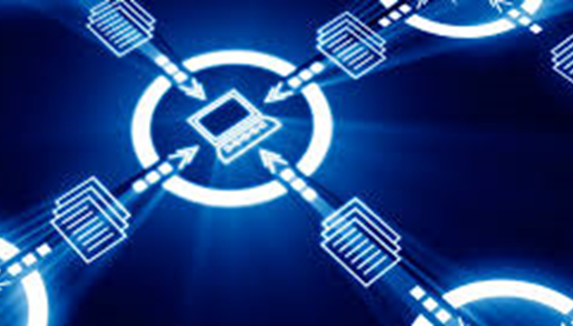
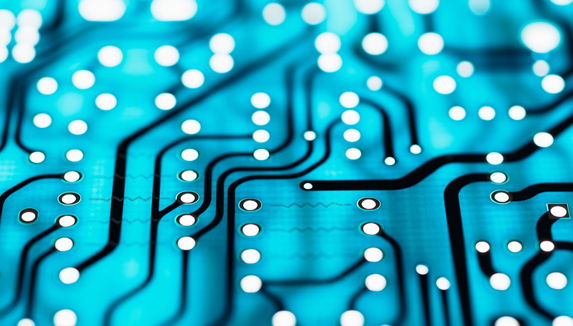
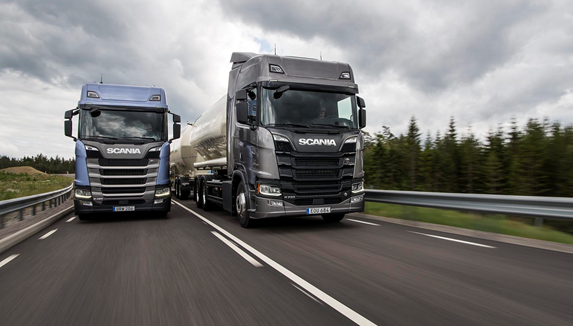
Logistics Manual
This Scania standard STD4172-1 states Scania’s EDI logistics requirements and is valid globally. As with all Scania Standards you can find them at the Scania Standards Application on Scania Supplier Portal.
EDI
EDI is mandatory for all organizations that supply automotive parts to Scania.
Scania’s first choice is always to set up a fully automated solution, but if that is not possible, Scania can also offer a Web EDI solution.
Classic EDI – Fully automated EDI
Scania’s basic policy concerning EDI communication is to use point-to-point communication between Scania and each supplying Organisation. Having fully automated EDI will give both parties substantial benefits when communicating.
Web based EDI
In general, Web-EDI is only to be used as an exception and if the organisation is supplying a small number of parts with low volume, since it´s a more manually process than the Classic EDI. Scania’s WebEDI provider is SEEBURGER.
NOTE!
Sequence suppliers must have point-to-point communication, WebEDI is not an option for this flow.
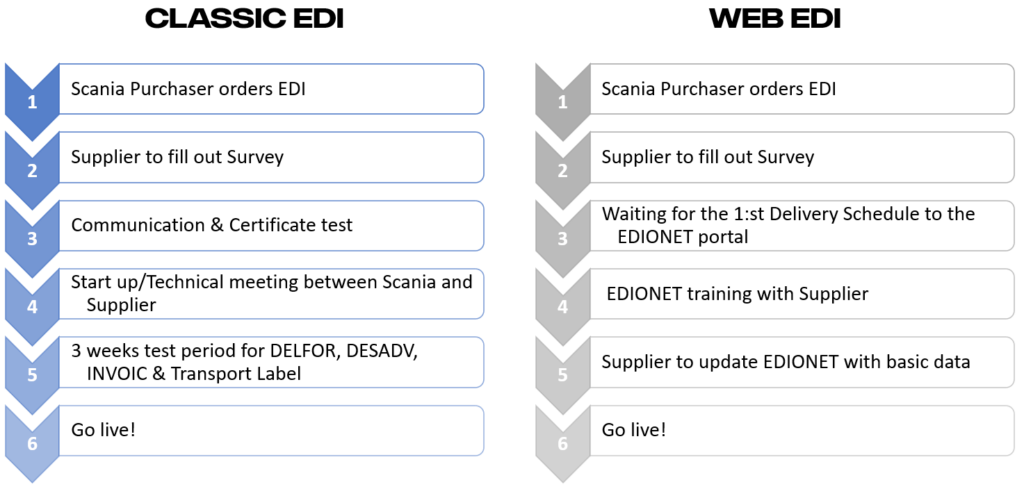